MPavilion 10 Uniform Commission
UNIFORM
BY DNJ PAPER
DNJ Paper – led by Daphne Mohajer va Pesaran and Jake Nakashima-Edwards – has been selected for the MPavilion 10 Uniform Commission. Composed of a green linen jacket with a pink paper vest worn on top, their uniform is inspired by a Japanese-style work coat called a samue.
‘We are always thrilled to uncover new designers to partner with on the creation of MPavilion’s uniform. DNJ Paper was chosen for the unique synergies they share with this year’s architect – their combination of natural materials with minimalist structure thoughtfully reflects Tadao Ando’s values and ideas,’ said Naomi Milgrom AC, commissioner of MPavilion.
We visited DNJ Paper in their studio at Hanover House to talk all things Uniform Commission.
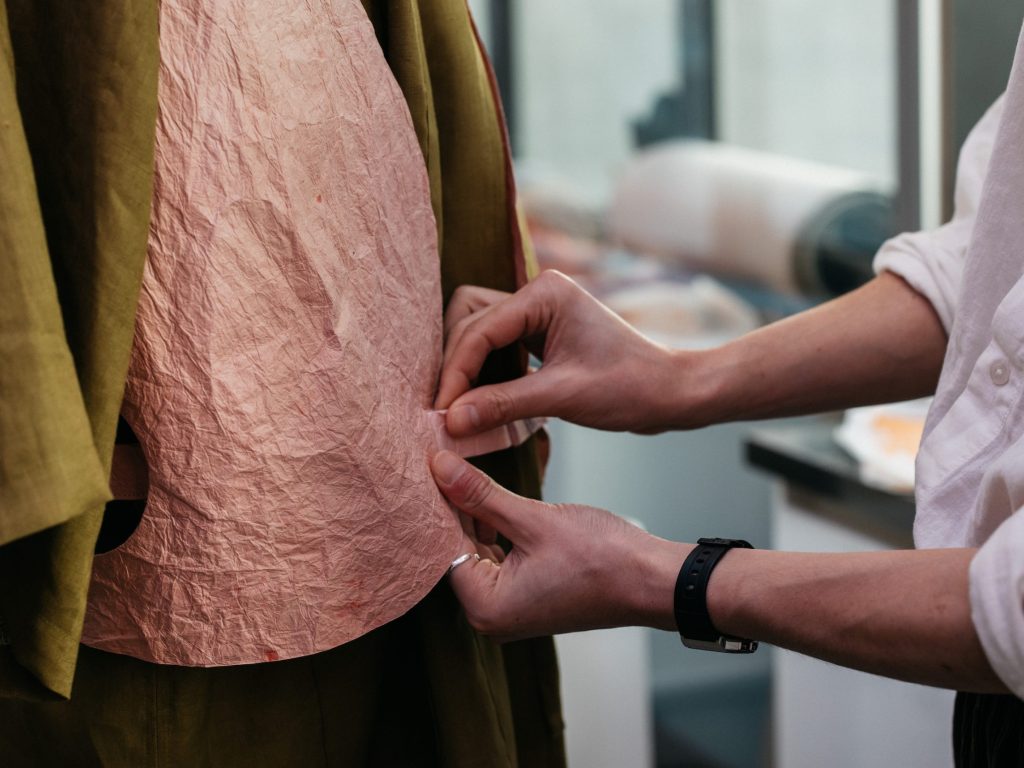
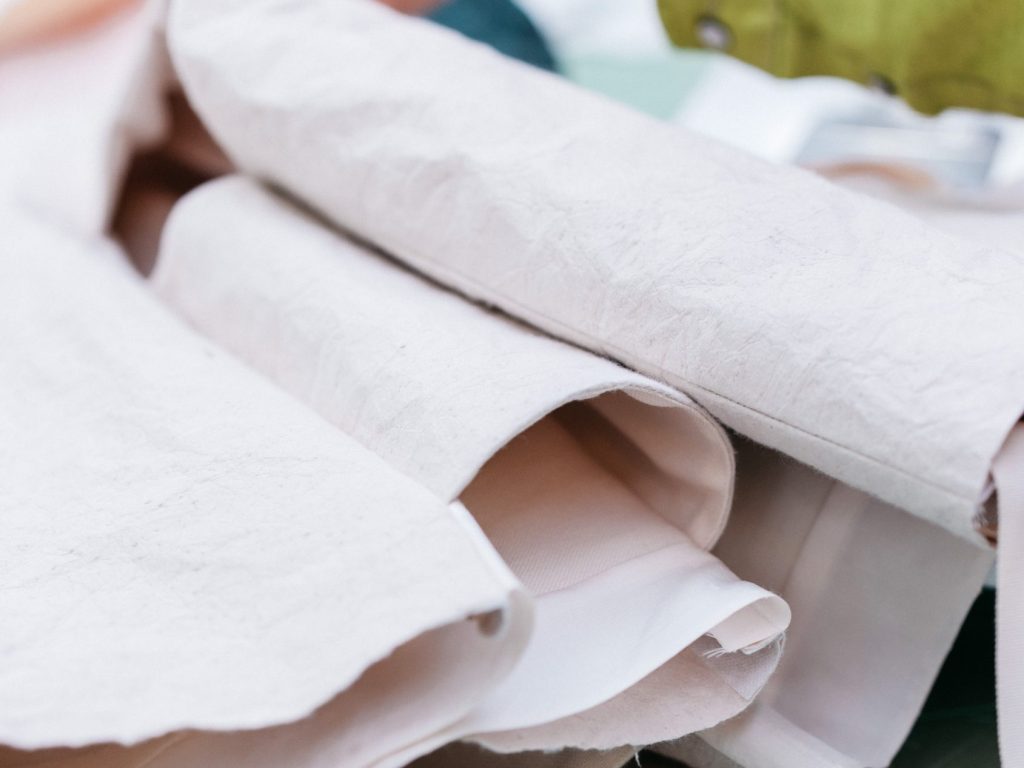
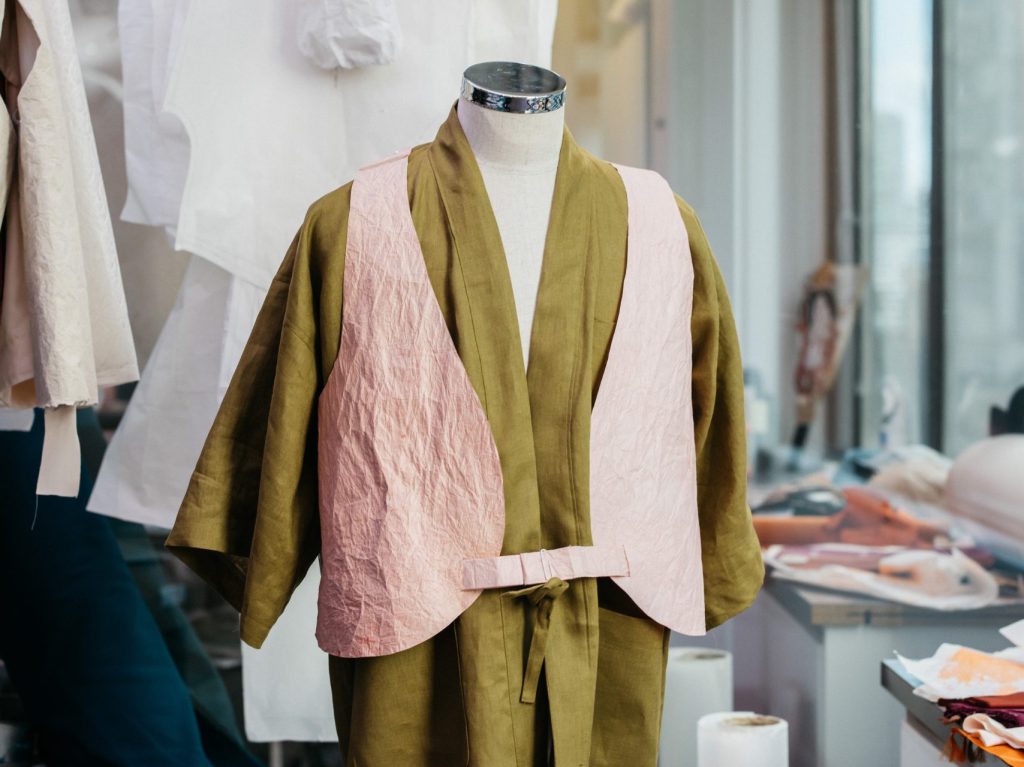
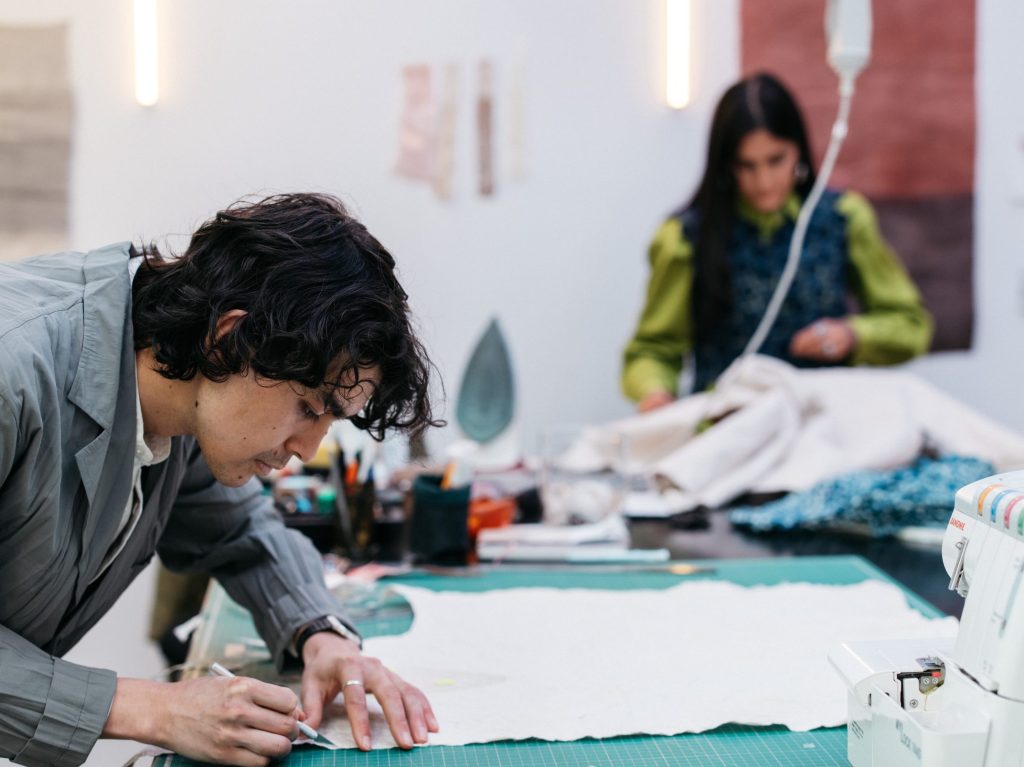
Q&A With
Dnj paper
Can you tell us about your paths to DNJ Paper? Individually, in terms of your passions and pursuits – and how you came together?
We came together via a shared interest in paper clothing, albeit from two perspectives. Jake was interested in speculating about the future potential of paper garments as hyper-fast fashion and Daphne’s area of research was in the historical contexts and techniques related to paper clothing in Japan. Daphne spent 10 years living in Japan and first encountered washi paper during her PhD research about material-making practices contingent on human-non-human relationships. She spent time with papermakers in their communal facilities and became fascinated by washi paper but noticed that not many people were engaged in the niche practice of wearing paper. Jake investigated washi as a textile during his Honours in Fashion Design at RMIT University, which proposed that a compostable, completely recyclable material like paper would be the ideal textile in the hyper-consumptive fast fashion era that we inhabit now. While approaching washi clothing from very different angles, we discovered that our values and ideas surrounding fashion were very aligned and, after working together on a project after Jake graduated, we became friends and have continued working together since.
Your practice is steeped in Japanese influence. Can you relay a little about your personal connections and experiences with the country and its culture – and your discovery of historical paper clothing there?
Daphne is Iranian-Canadian. She moved to Japan in 2008, spent 10 years there then met an Australian partner and now calls Melbourne home. She discovered the history of paper clothing by chance then joined the local historical societies to learn more as there is very little research done on the topic, in Japanese or English. She’s undertaken a number of research projects on the topic, including one for the British Museum’s Endangered Material Knowledge Program, where she works to record and communicate knowledge on the topic of paper clothing in Japan before it disappears. This project focused on a small town called Shiroishi, but also took her to Tōdai-ji, a temple in Nara, which is the last remaining place where paper clothing is worn.
Jake is Japanese-Australian, and his Japanese family’s involvement in the textile arts had a strong influence on his interest in fashion and textiles. Working with washi and continuing the practice of paper clothes-making strengthens his connection to his other home.
Some might be incredulous at the idea of paper clothing in terms of feeling, cleaning, durability. Why paper and how might you respond to those doubts?
Being selected for this commission is an immense honour. It will be really exciting to see our work set alongside that of a legendary architect and consider how our paper garments perform over the course of a season.
Paper is an unfamiliar material for clothing, so people might be surprised by it at first, but we want to show its durability and potential for use in everyday life. It is a material that defies all logic when it comes to clothing, but perhaps clothing shouldn’t last forever, and change over the course of time. If fashion itself is beholden to seasonal changes, then why should garments themselves be immutable?
Can you share a bit about the source of the paper used in the MPavilion 10 Uniform Commission? How did you uncover Ueda and how do they work?
We are using handmade washi paper made by a family-run papermaking atelier called Ueda Handmade Washi Factory in a small village in Okayama, Japan. The paper made in this region is called Yokono-washi. The Ueda family has been engaged in papermaking for roughly 250 years and is the last family making the ultra-thin sheets of washi paper used for gold-foil stamping. Though that is their speciality, they are also capable of making exquisite paper of differing thicknesses, so we asked Yasumasa – the seventh-generation papermaker currently producing paper at the factory – to custom-make these sheets for us. The pulp is made from the inner bark of the Mitsumata tree, which was sourced locally from the mountains around the workshop. Mitsumata paper is off-white, so we will colour the paper to a rich pink using dye extracted from deadstock red polo shirts (uniforms we found).
Daphne was introduced to Ueda on a recent trip to Japan by Emilie from Hariko Washi and Yano from Pride of Japan; both are companies that work hard to create connections between washi makers and customers overseas. She visited the Ueda household and was able to see the extraordinary quality of the paper they produce as well as the conditions of production in their home studio.
What makes paper washi?
Washi paper is distinct from other kinds of paper in a number of ways – washi is made from kōzo (Broussonetia papyrifera), mitsumata (Edgeworthia chrysantha) and gampi (g. Wikstroemia). It’s much stronger and flexible than typical paper such as that used for a notebook page or receipt and is suitable for many applications in daily life, from architecture to clothing.
Can you conjure the process through which the Uniform Commission is created? What happens at each and every step – which parts are tradition and innovation?
The uniform consists of a green linen Japanese-style work jacket called a samue and a pink paper vest. Each uniform will use one sheet of paper and be dyed using runoff dye from old shirts, then stitched and finally waxed with Australian beeswax to make it water-resistant and strong. We use the same waxing technique on our paper baseball caps, which have survived stress-testing in the rain, at the beach and during hot Australian and Japanese summers. This will be our first time waxing an entire garment – an engineering challenge, but we are up for it!
You’ve dreamed up the Commission from your studio at Hanover House – on a floor designed by Sibling Architecture within a building emblazoned with Atong Atem’s art. Can you tell us a bit about this experience working at the intersection of architecture, art and design – and alongside other extraordinary makers?
It’s been an absolute dream working in this space. We’ve been given the freedom to explore our practice in the widest sense materially (through dyeing, printing, papermaking) as well as contextually (running workshops, considering the future of retail, impact of waste). We’ve also had the chance to show our work to a wider audience and experience the immense positive response – and the questions! The top three we get are: Paper? Yes. Can it get wet? Yes. Can you wash it? By hand or dry-clean, yes.
Working with the other artisans in the space (Ella Saddington and Jessie French), BETA’s Creative Director James Hewison and the entire team from the Future From Waste Lab has also been an inspiring and encouraging learning experience. The conversations and collaborations, be they small or robust, that have emerged from this shared working space have been invaluable to us.
You have an exhibition coming up at Craft Victoria. Can you give me a glimpse into what it might entail?
Our exhibition at Craft Victoria explores paper as an alternative to conventional cloth. The forms of paper that surround us – smooth, white, easily torn and weak to water – are typically made from the flattened, bleached fibres of wood pulp. Kamiko: Five Paper Coats is a sequence of five jackets assembled from sheets of wrinkled handmade Japanese washi paper sourced from workshops in Kurotani, Mino and the Noto peninsula that show very different material possibilities of paper. These garments are made of five unique papers – a paper that includes clay and diatomaceous earth, cedar bark paper, eucalyptus-dyed paper, traditional paper cloth treated with konnyaku jelly, and lace paper.
Finally, how does the Uniform Commission respond to Tadao Ando’s design – how do you foresee it enlivening this momentous space?
The design was inspired by Japanese workwear. We typically produce custom made-to-order garments from handmade washi paper, so designing a paper uniform was a unique challenge for us. It has evolved a lot as we’ve been making samples and considering how the paper will wear and tear over the course of the summer, and how it will fit on bodies of varying proportions. Some elements of the design, such as the circular area with the adjustable strap, were designed in response to the forms in the pavilion.
In the context of Ando’s design, we chose fine, lightweight linen to respond to the concrete and wrinkled, waxed paper to bring texture to the space. This year has something rare for MPavilion designs: walls that separate inside from out. The colours for the uniform were chosen in consideration of this setting and the colour of the concrete structure – we hope to bring some garden colours inside the structure.
The MPavilion 10 Uniform Commission: DNJ Paper will be worn by members of MPavilion’s front-of-house team during our free, five-month design festival, 16 November 2023 – 28 March 2024. It will also be exhibited in Kamiko: Five Paper Coats at Craft Victoria from 14 September – 28 October 2023.
The MPavilion Uniform Commissions have won a number of awards, including: Best in Category, Fashion Design – MPavilion 7 Uniform Commission, Victorian Premier’s Design Awards (2021).
Previous
Commissions
MPavilion 9: SAFA EL SAMAD
Cotton drill.
Designed by Safa El Samad.
A second-generation Lebanese Australian who lives by the axiom ‘the architect should be able to design everything from the city to the spoon,’ El Samad designed a convertible apron-tote for her Uniform Commission. Her design features embroidery inspired by all(zone) & their MPavilion 9 design. Learn more here.
Photograph by Marie-Luise Skibbe.
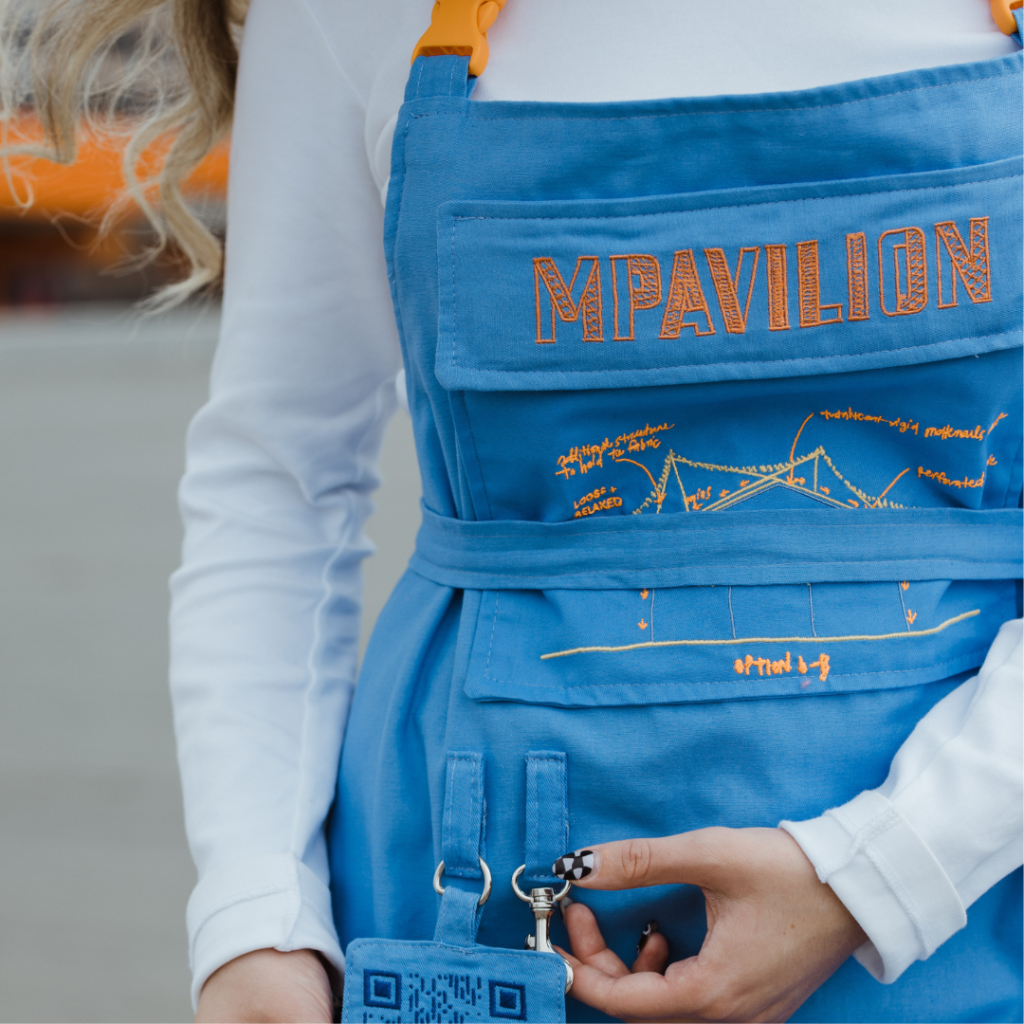
MPavilion 8: Erik yvon
Hand-printed cotton.
Designed by Erik Yvon.
Inspired by his origins in Mauritius and the MPavilion 8 program theme of ‘island life,’ Yvon created a bespoke print for the MPavilion 8 Uniform Commission which drew on fond childhood memories of fishing trips with his father. Learn more here.
Photograph by Marie-Luise Skibbe.
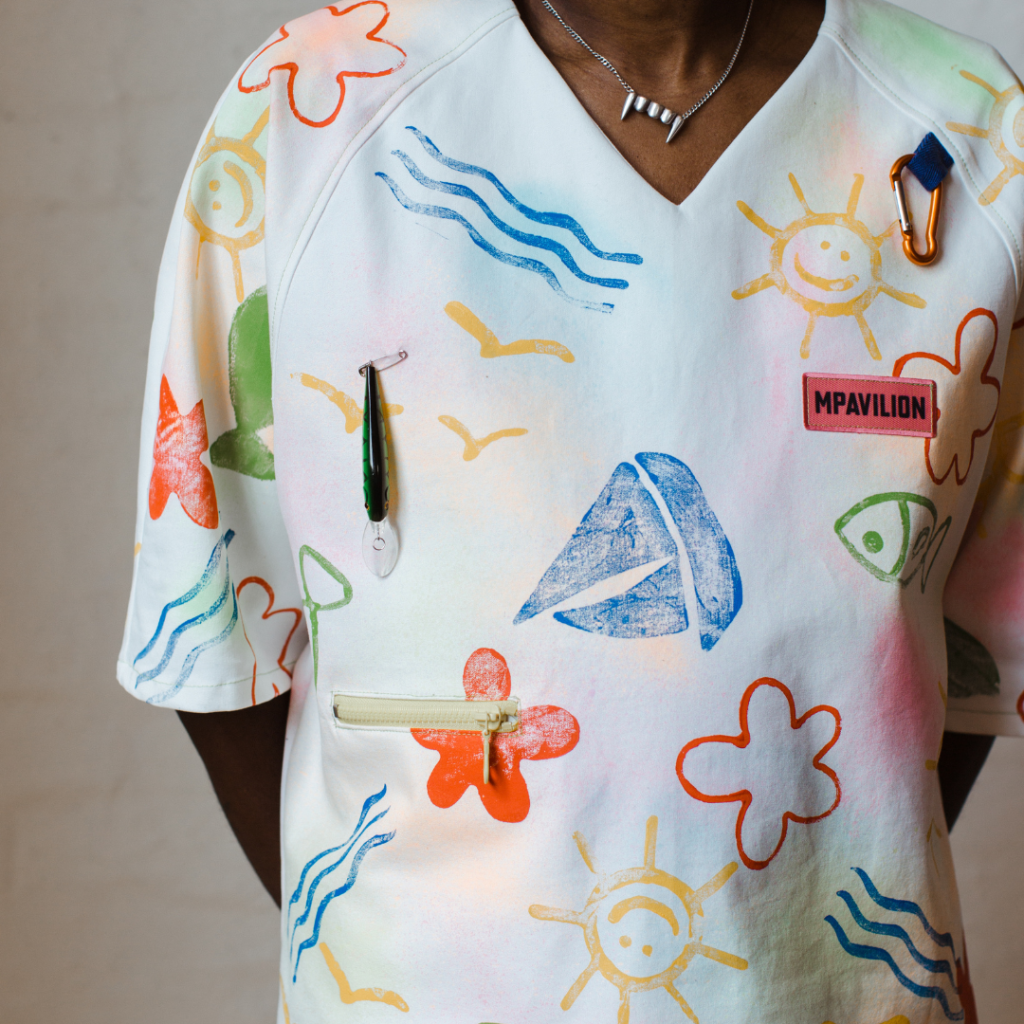
MPavilion 7: chelsea hickman
Materials from previous MPavilion Uniform Commissions.
Designed by Chelsea Hickman AKA Fashion Chelsea.
Upcycled from uniforms of seasons past, the garments Hickman created include over-layer lab coats, under-layer T-shirts & reusable face masks. All were custom-made, with each piece unique and ethically produced. Learn more here.
Photograph by Jesse Essy.

MPavilion 6: THE SOCIAL STUDIO & Beci orpin
Recycled material and cotton.
Designed by The Social Studio and Beci Orpin.
The Social Studio worked closely with MPavilion to design this Uniform Commission’s boiler suit, with Beci Orpin conjuring a colourful and functional utility belt to complement it. Learn more here.
Photograph by Marie-Luise Skibbe.
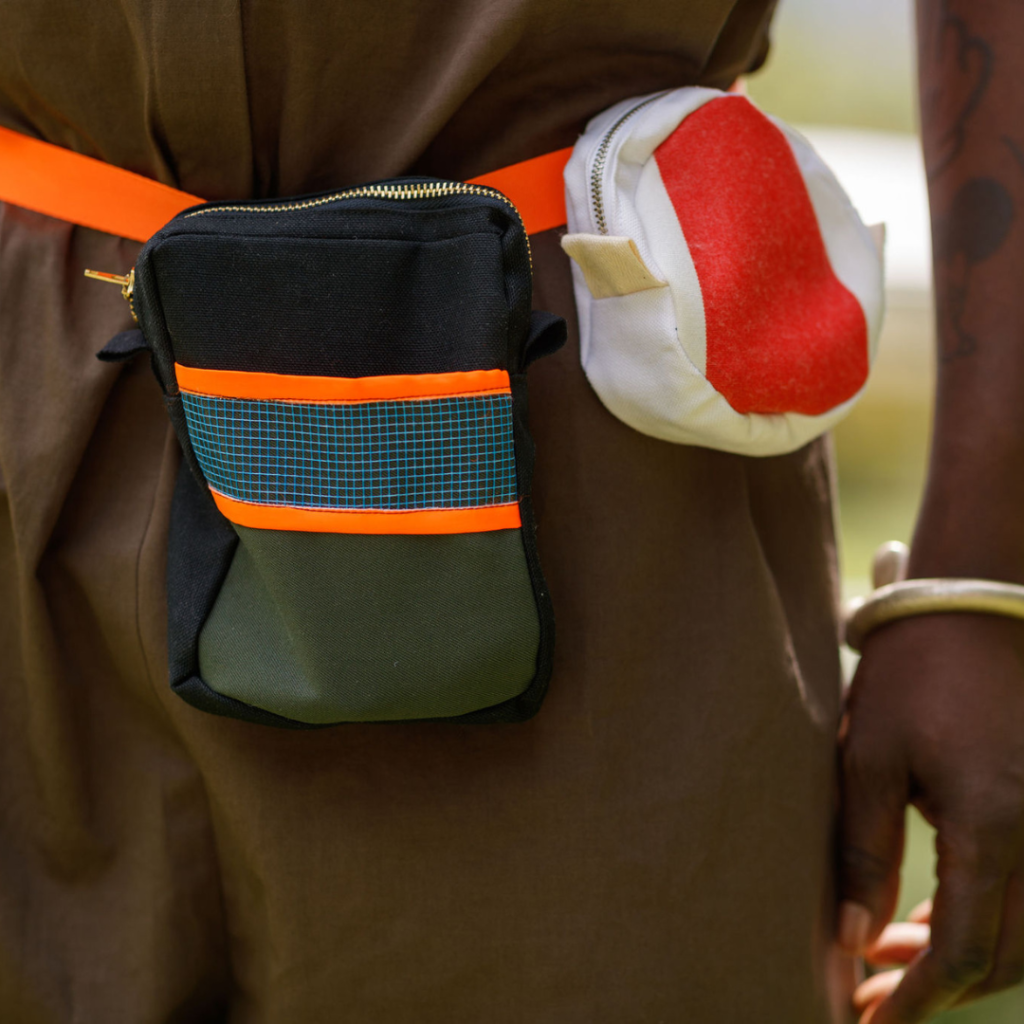
MPavilion 5: ESTHER STEWART
Canvas and neon trim.
Designed by Esther Stewart, made by Hannah McMullin.
Inspired by cycling and fishing nets, this utility-style Uniform Commission blends cutting-edge design with grounded practicality. Stewart also created a Fold, Play – an interactive art installation – for MPavilion 5. Learn more here.
Photograph by Marie-Luise Skibbe.
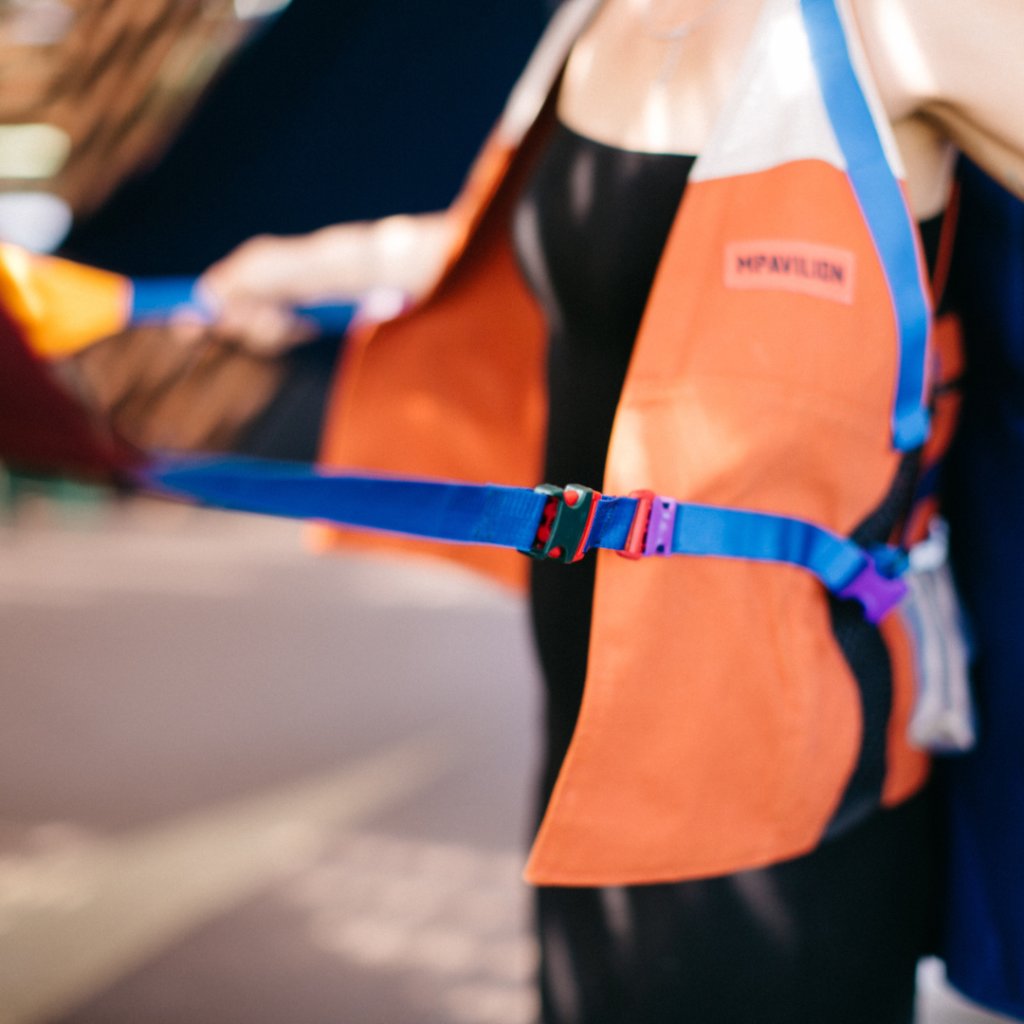
MPavilion 4: STUDIO ONGARATO
Metal.
Designed by Studio Ongarato.
A series of Rem Koolhaas quotes inspired by OMA themes were reproduced on badges designed by Studio Ongarato and attached to bespoke T-shirts worn by the MPavilion 4 front-of-house team.
Photograph by Tom Ross.
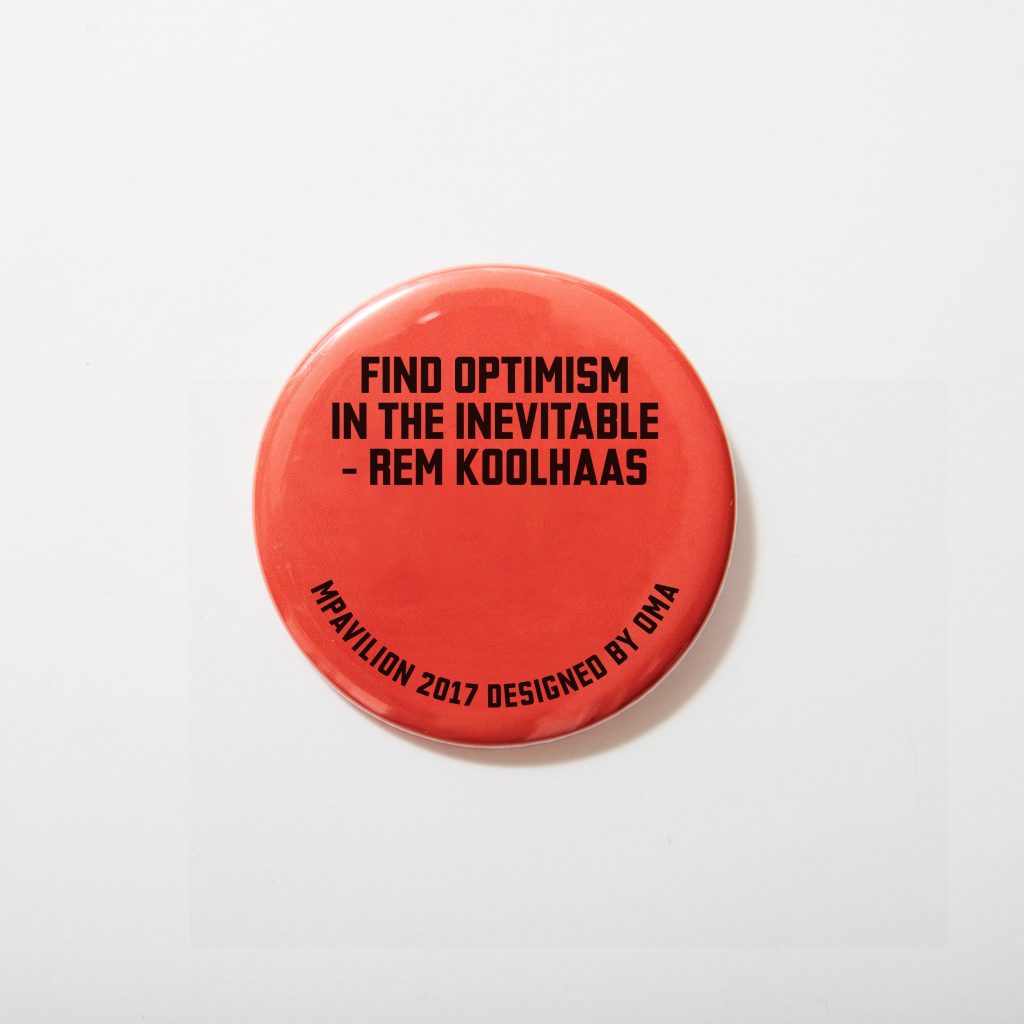
MPavilion 3: P.A.M.
Cotton.
Designed by Perks and Mini AKA P.A.M.
Mischa Hollenbach and Shauna Toohey of Perks and Mini AKA P.A.M. created a one-off print for an MPavilion 3 Uniform Commission T-shirt. They paired this with classic Australian work staples from Hard Yakka customised with patches and appliqué. Learn more here.
Photograph by Tom Ross.

MPavilion 2: KLOKE
Cotton.
Designed by Amy and Adam Coombes of Kloke.
The MPavilion 2 Uniform Commission was adapted from Kloke’s Good Sport collection, which conjured a sense of perseverance and aspiration through its light fabrics and natural, earthy colours. The ink navy colouring and bold grey mélange lines responded to A_LA’s translucent petal design. Learn more here.
Photograph courtesy of Kloke.
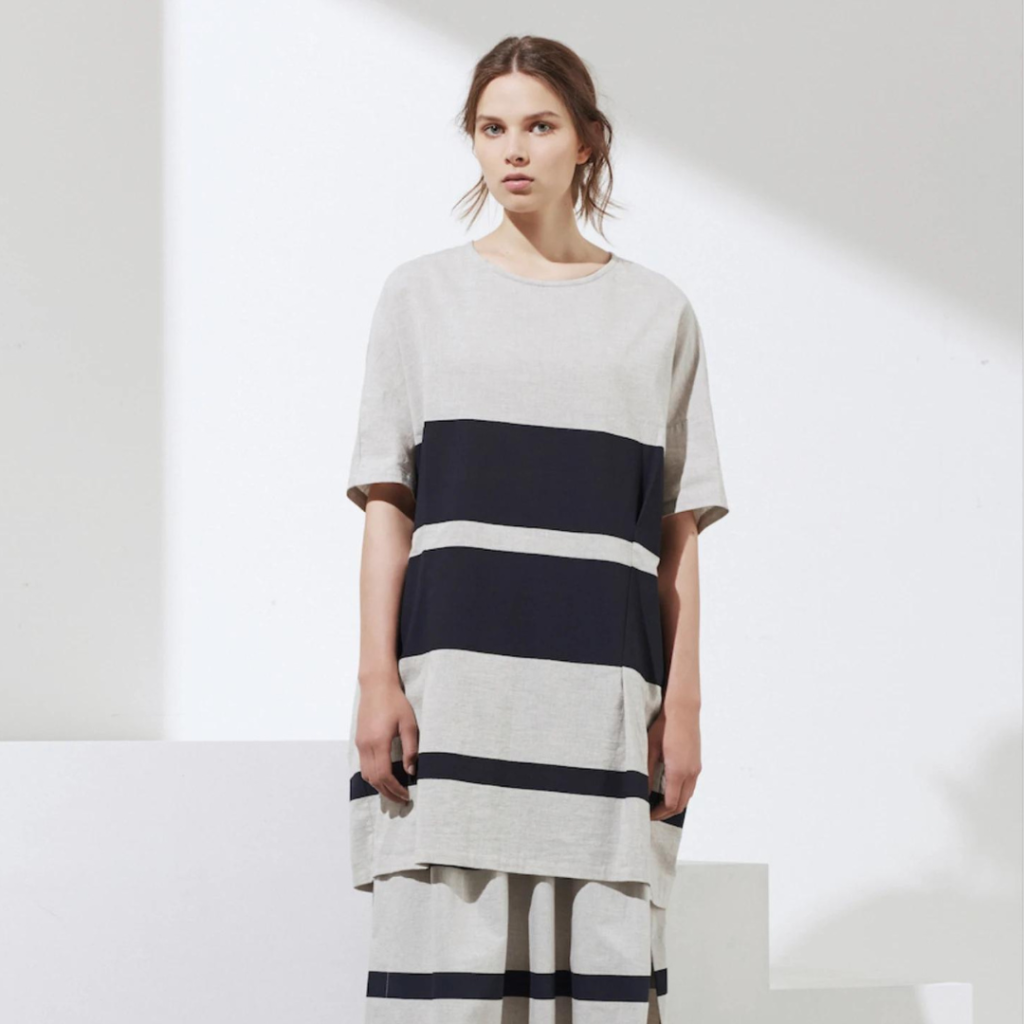
MPavilion 1: ALPHA60
Cotton.
Designed by Alpha60.
This Uniform Commission’s aprons, T-shirts and skirts (Alpha60 also created bags and cushions for the inaugural MPavilion) were a response to the perforated screens of Sean Godsell Architects’ pavilion. Alpha60 will return to the Queen Victoria Gardens for an extraordinary performance during MPavilion 10.
Photograph courtesy of Alpha60.
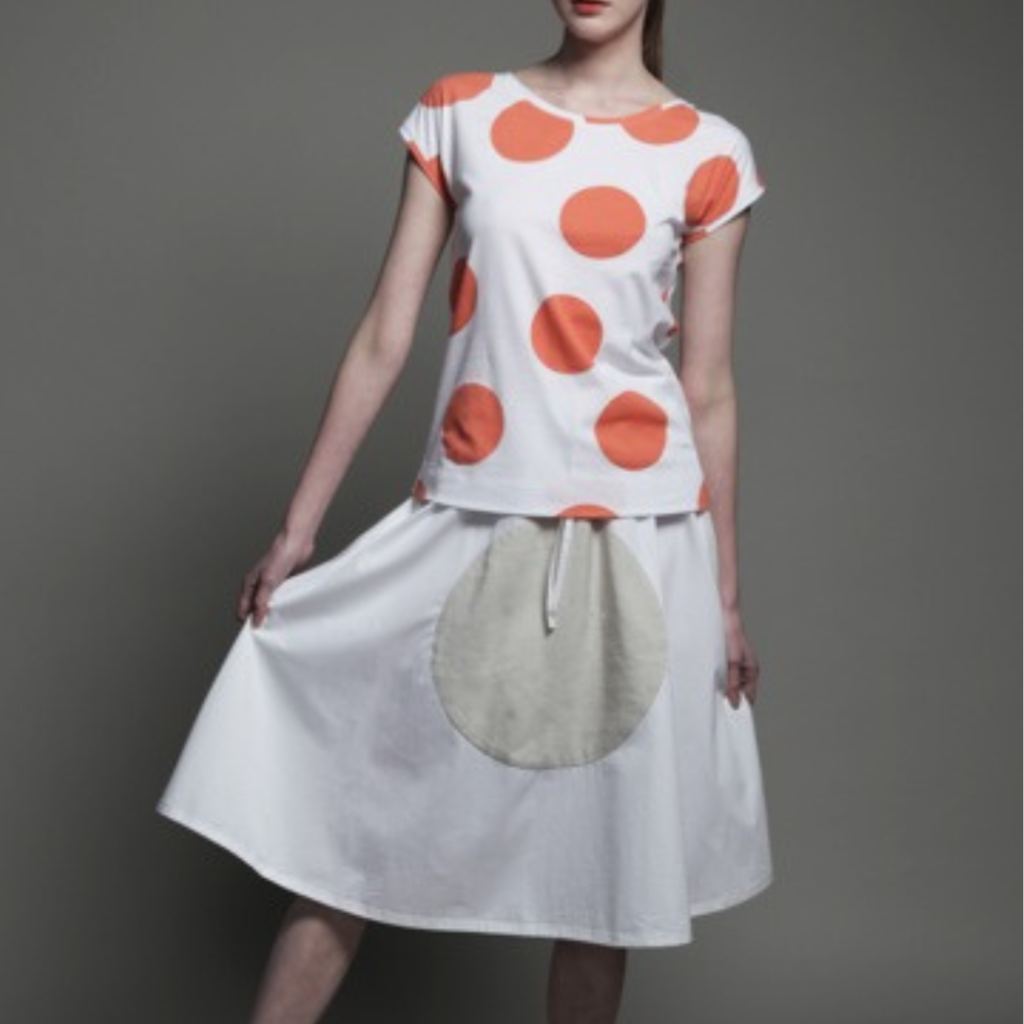